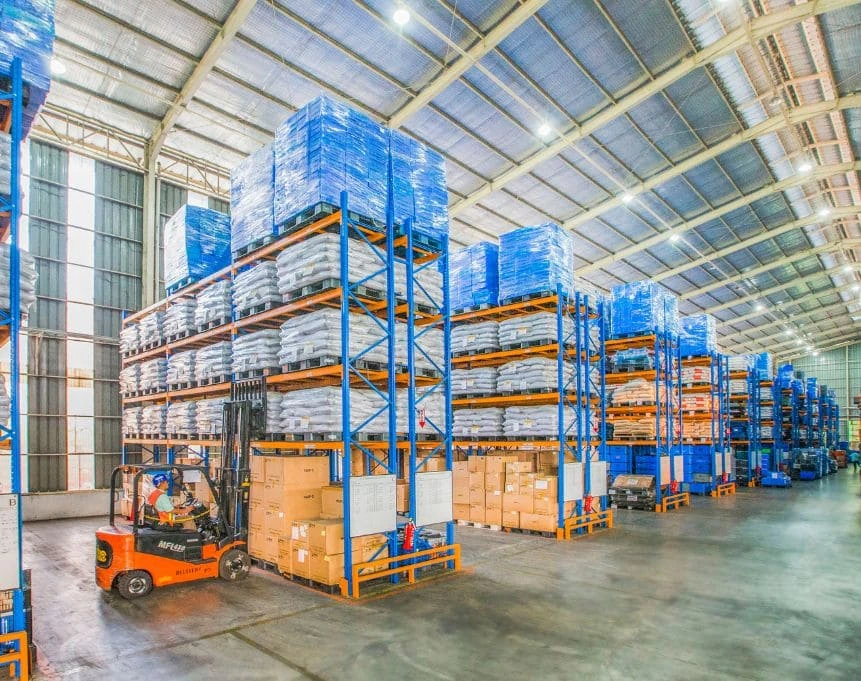
How To Do Space Optimization with Pre-Engineered Buildings for Warehousing
A PEB’s Main Weakness in Warehousing Optimization
A logistics company was having a hard time. Their warehouse became a bottleneck because online orders surged. Forklifts struggled to pick products efficiently while maneuvering through narrow aisles. Available space was underutilized, even though storage racks were brimming to the max.
There was an obvious solution: to expand. Unfortunately, traditional construction came with expensive, lengthy timelines, and rigid layout options. The company needed faster, flexible alternatives that were also cost-effective.
The company is not alone. Businesses across the e-commerce, automotive, FMCG, and pharmaceutical industries face the same challenge: how to maximize warehouse space without costs increasing.
Pre-Engineered Buildings (PEBs) offer a revolutionary solution by enhancing space efficiency, reducing construction times, and providing scalable storage options that are not bound by the limits of conventional buildings.
PEB’s space optimization strategies will be the focus of this guide, ensuring your facility meets both current and future business demand.
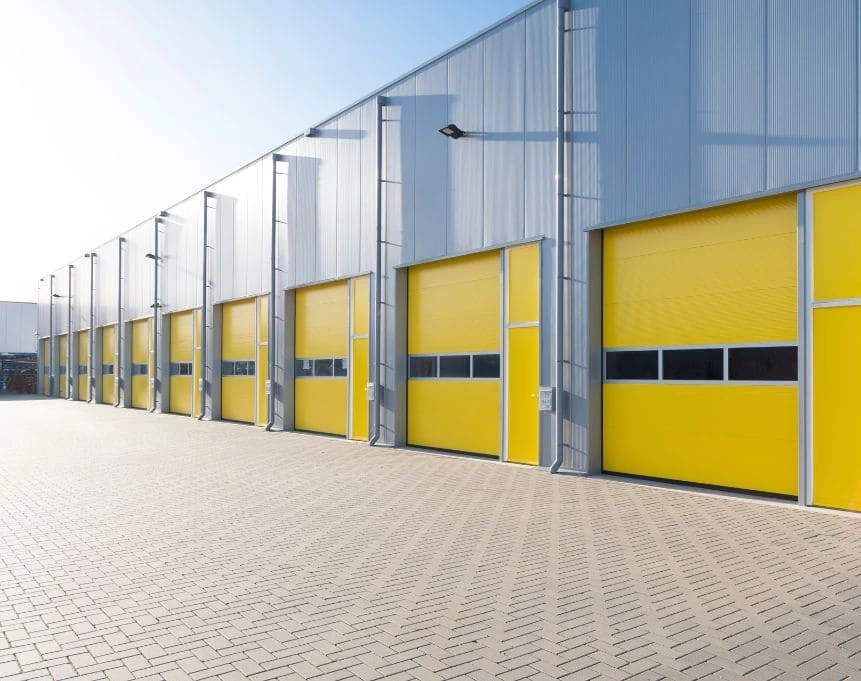
Why Space Matters for Optimization in Warehouse Systems
Used to store products, warehouses play a critical role in supply chain operations. Every square foot of a warehouse that is unused costs money, delays orders, and makes operations less efficient.
Consequences of poor warehouse optimization:
- Vertical space waste due to unoptimized cubic footage.
- Delays in inventory flow from ineffective aisle configurations.
- Increased real estate spending from relocating instead of redesigning.
With soaring industrial land costs in India, optimizing warehouse space is vital. Pre-engineered steel warehouses solve this with customized layouts, advanced racking systems, and expandable designs.
How Do Pre-Engineered Buildings (PEBs) Adjust Spaces in Warehouses?
1. Improving Vertical Space Efficiency
Ignoring vertical space is a common warehouse design error. PEBs address this with:
- Clear-span construction (no internal columns) for vertical storage.
- Custom ceiling heights for high racking systems.
- Mezzanine floors to double usable space.
Result: 50%+ storage capacity within the same footprint.
2. Modular Layouts for Expansion
PEBs enable:
- Adding organizational bays without major renovations.
- Tailored layouts for bulk storage and heavy-duty needs.
- Easy transformation of office space, loading docks, or specialized zones.
3. Optimized Floor Plans for Efficiency
PEBs allow:
- Wider aisles for forklift maneuverability.
- Strategic dock placement to save loading/unloading time.
- Integration of automation (conveyor belts, robotics, AI).
4. Cost-Effective & Fast Construction
PEBs reduce construction time by 50% and costs by 20-30% through:
- Prefabricated components lowering on-site labor.
- Lightweight steel cutting material costs.
- Energy-efficient designs reducing long-term expenses.
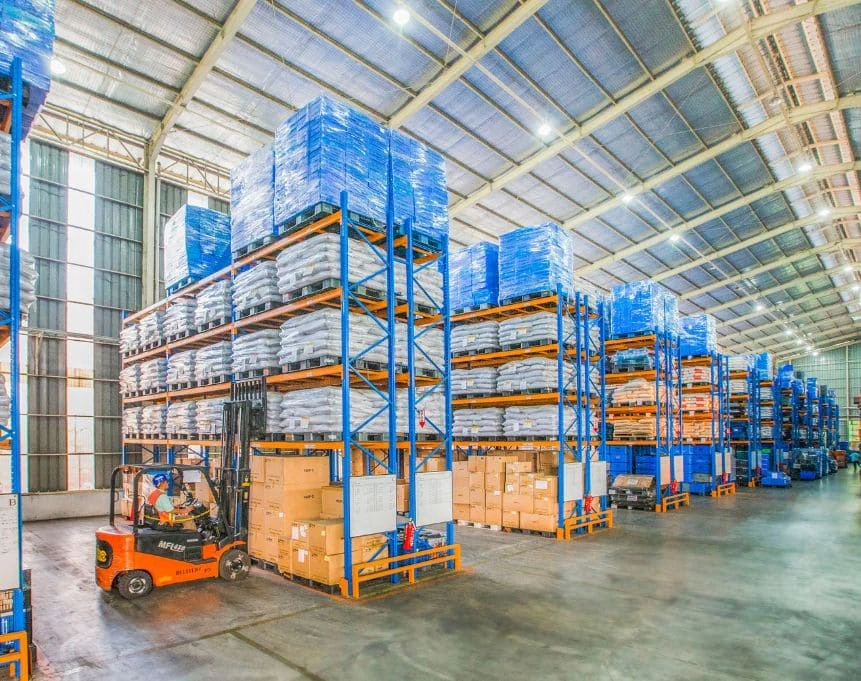
Innovative Storage Techniques for PEB Warehouses
High-Density Racking Systems
- Selective Racking: Ideal for diverse goods.
- Pallet Flow Racks: Maximize bulk storage.
- Cantilever Racks: Store long/atypical materials.
Mezzanine Floors
- 2-3x storage capacity without new construction.
- Convert upper floors into offices or workspaces.
Optimized Aisle Widths & Traffic Flow
- Adjust aisles for forklift navigation and safety.
- Streamlined workflows reduce congestion and accidents.
Industries Using Pre-Engineered Warehouses in India
- Retail & E-commerce: High-volume storage and fast fulfillment.
- Pharmaceuticals: Temperature-controlled storage.
- Manufacturing: Raw material and finished goods storage.
- Food Processing & FMCG: Hygienic bulk storage.
- 3PL & Logistics: Customizable distribution centers.
Optimize Your Warehouse Space with Metal Tree’s Solutions
Metal Tree specializes in custom PEB warehouses for Indian businesses.
Why Choose Metal Tree?
✅ Space optimization with vertical/horizontal designs.
✅ High-quality steel structures with low maintenance.
✅ Faster ROI from reduced downtime and costs.
✅ Energy-efficient designs for long-term savings.
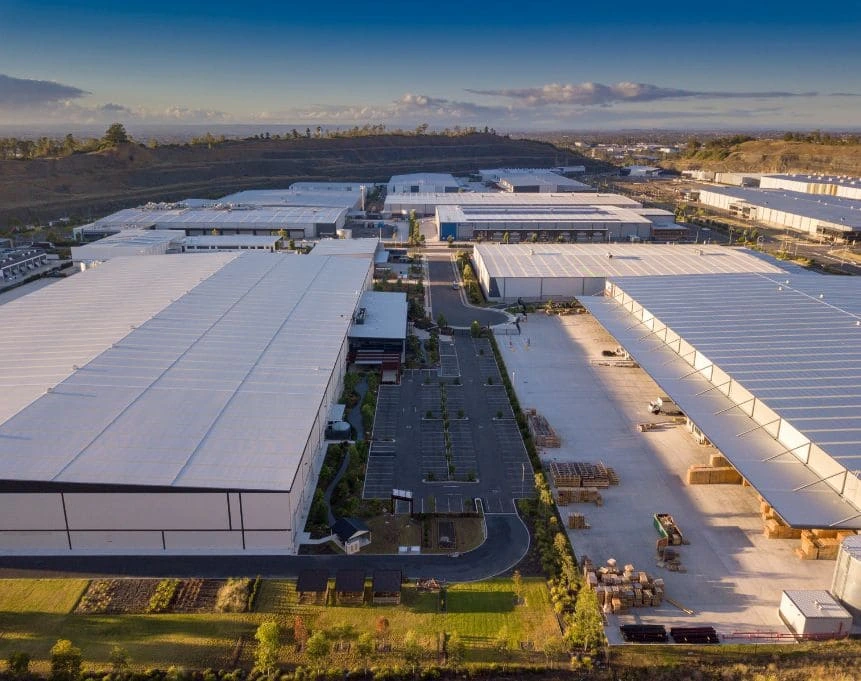
“At Metal Tree, we believe that warehousing should be smarter, not just bigger. Our Pre-Engineered Buildings (PEBs) are designed to maximize space, enhance efficiency, and reduce costs—helping businesses scale seamlessly while optimizing every square foot. The future of warehousing isn’t just about expansion; it’s about intelligent, adaptable, and cost-effective solutions. Let’s build that future together”
Final Thoughts: The Future of PEB Warehouses
PEB warehouses are transforming India’s logistics sector with:
✔ Scalable storage solutions.
✔ Lower operational costs.
✔ Future-proof adaptability.
Key Takeaways:
- Boost storage capacity with vertical solutions.
- Slash costs with energy-efficient upkeep.
- Enhance workflow with smart layouts.
Ready to upgrade?
📞 Contact Metal Tree for custom PEB solutions tailored to your needs!
One thought on “How To Do Space Optimization with Pre-Engineered Buildings for Warehousing”
Add a Comment Cancel reply
All Categories
Recent Posts
Benefits of Pre-Engineered Buildings for Industrial Facilities in India
Prefabricated Steel Buildings for Commercial Construction in India
Benefits of Pre-Engineered Steel for Construction Projects
Tags
Call Us at
+91 9311624628
[…] lightweight nature of PEBs (pre-engineered buildings) does not compromise their strength, which is one of the primary reasons they are favored in […]